There are many factors that can affect the cost of running a warehouse. The size of the warehouse, the location of the warehouse, and how much inventory is being stored all play a role in determining how much it costs to run a warehouse. For example, the cost of running a warehouse will depend on the size of the facility, whether it is located in an urban or rural area, and how much inventory is being stored. Owning and managing a warehouse can be extremely costly, but being aware of the tips listed in this article may help you to reduce some of your overhead and make your warehouse more efficient at the same time.
Owning and managing a warehouse is costly
As of 2020, the average cost of running a warehouse per year per square footage was $7.81 — on top of that, the average starting hourly rate of basic warehouse staff was $13.47. Running a warehouse is extremely costly.
Many expenses come with warehouse maintenance and running. The most expensive of them all is the cost of labor. Other expenses include electricity, water, and other utilities. It is important to note that there are many ways to cut down on these expenses including using a more efficient lighting system, using solar power to generate electricity, and using water-efficient fixtures.
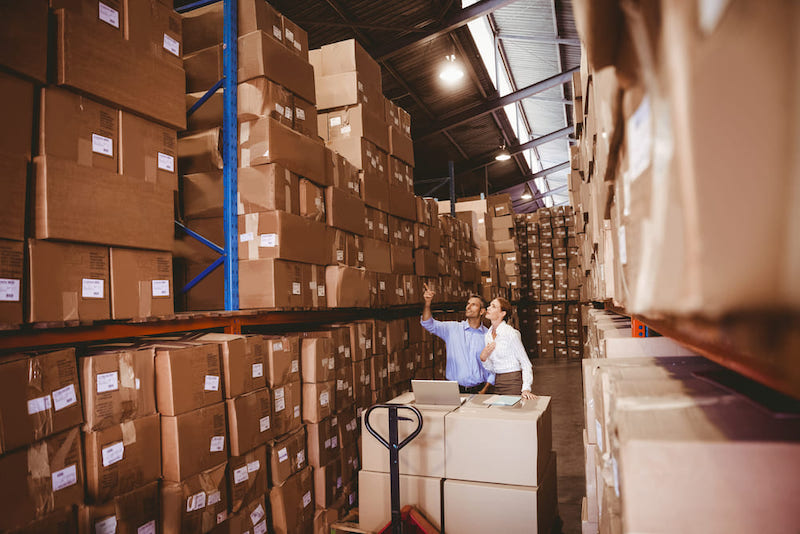
Your biggest overhead comes from your employees and what you have to pay them — not to mention the conditions you have to continually give them in order to stay true to federal protocols. For example, just so most managers get a clear idea of costs associated with staff, more than 60% of operating costs in a Distribution Center or warehouse can be attributed to order picking. Why is that? Order picking is the costliest among all warehouse processes because it tends to be very labor intensive — in most cases, it focuses on manual picking. By automating picking, warehouses can control and even reduce by half – once the initial investment and upfront capital of the tool has been recuperated – their operational budget.
Typical warehouse expense
Warehouse expenses are the costs that are incurred by a business in order to store goods in a warehouse. They include a wide variety of tools, factors, and services. Not only tangible ones but intangible ones.
Among the tangible ones we can pinpoint:
- Rent.
- Taxes.
- Depreciation of warehouse assets.
- Maintaining facilities and warehouse tools.
- Staff.
Meanwhile, Intangibles are the costs that are incurred because of a business’s investment in ethereal assets, such as goodwill, branding, PR, and intellectual property.
How to reduce warehouse costs?
Today, in order to properly have a successful warehouse, managers and investors need to do two things.
- Increase their productivity.
- Decrease their operational costs.
Maximizing profits is an essential part of what is needed to survive in today’s ultra-competitive environment. It requires not only a carefully executed and planned strategy but the ability to objectively analyze and auto your business and cut out the dead weight while streamlining current processes.
Let’s look at some ways managers can achieve this.
Reduce space by optimizing storage
It might seem like something obvious to reduce warehouse costs but it is complex and difficult to perform. Today, it is integral to save space while also having stockpiles of essentials, and being flexible. The successful optimization of warehouse space is vital for an agile and highly productive supply chain. Consider the following:
- Physical structure.
- Warehouse flow.
- Storage.
- Retrieval methods.
- Product placement.
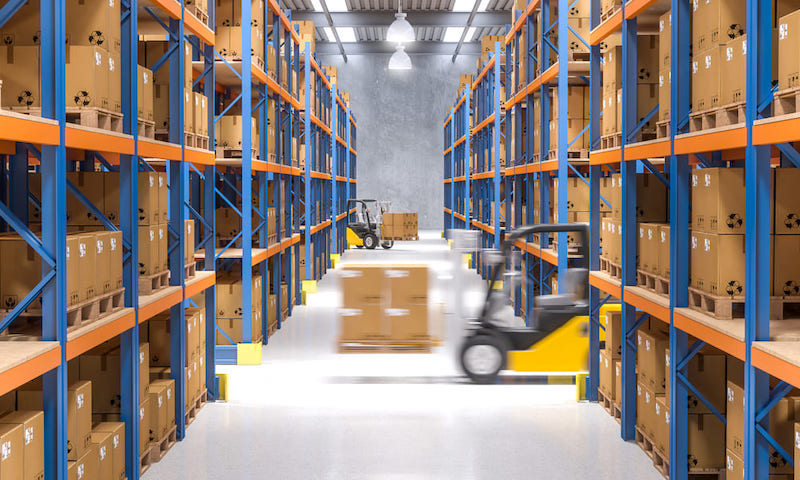
Audit your warehouse’s principle layout, align flow with product and volumes, and design a material handling strategy that takes into account equipment as well as people. Use metrics and data analysis management systems to truly map out your warehouse.
Warehouse automation
Surveys have continually shown that 74% of employees demand automated services — they improve their job satisfaction by editing out repetitive tasks. Using good-to-robot innovations and drones, mixed with AI-sponsored software can boost your DC efficiency and reduce warehouse operating costs. For example, manual picking methods allow workers to handle approximately 75 to 150 items per hour, while automated tools, such as drones, can supercharge this process — between 200 to 800 items in the same time frame.
Warehouse automation will not only increase your productivity but will decrease labor costs. Another great advantage is that a fully automated warehouse can work 24/7 with a skeleton crew.
Create an inventory review process and eliminate excess inventory
Today, due to the disruption of supply chains, most warehouses are overstocking items and products. It’s a Catch-22 dilemma. On one hand, they have to eliminate excess inventory, on the other hand, they need to have key items in place just in case. It’s critical to have predictive tech and inventory visibility across your entire supply chain.
By implementing software and AI tech, warehouses can reduce costs while also increasing their accurate forecasting capabilities, their efficiency, and successfully fulfilling current demands.
Protect your inventory
A warehouse can lose millions of dollars due to fire or theft. It’s critical to prevent huge losses and cut back on inventory costs. It’s paramount to track items and stay on top of red flags to identify culprits or scenarios where your stock might be in danger.
Some red flags include:
- A sense of entitlement among certain crew members.
- Stock levels that don’t match sales records.
- Rumors of theft.
- Dip in sales.
- Missing or unusual invoices.
- Stock is constantly discovered in the workplace.
By combating theft, and protecting your inventory, you not only promote awareness within your staff but cut back on the cost associated with restocking items that were stolen.
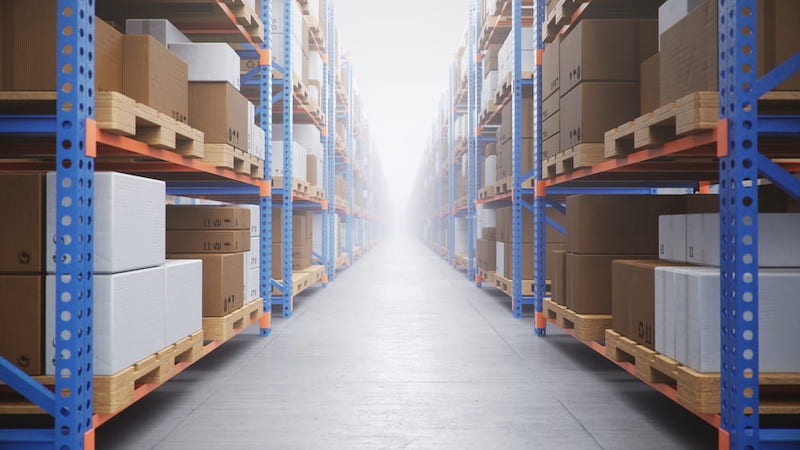
Optimize your process
Part science, part imagination mixed with creativity, optimizing your process on all levels is essential for reducing warehouse costs. From integrating cross-docking to fulfilling on-demand desires and consumer trends. Today every little bit counts. Warehouses can reduce their costs by thinking outside the box.
Some warehouse cost-saving ideas that take into account optimization include:
- Merging transit.
- Understating that High-quality goods do not need a quality inspection.
- Pre-tagging ideas.
- Not mixing SKUs.
- Prioritizing urgent and VIP orders.
- Ensuring stock is labeled properly.
- Using WES or WMS systems.
- Avoid vertical picking wherever possible.
- Placing larger and heavier inventory towards the back of your warehouse.
- Cutting back on perishable items.
Where to not cut back?
Oddly enough, the one warehouse cost-saving idea we recommend spending on is technology — innovation and automating demand a huge cash infusion up front, in some cases a vast investment, but the ROI is staggering. If you can avoid it, never, ever reduce warehouse costs by sacrificing your competitive nature and your ability to future-proof your business.