A warehouse’s sorting strategy and processes have slowly become one of the key challenges of today’s supply chains. And why is that? Because consumers, clients, and other figures in our overall model demand one thing above everything else — Speed. They demand everything to arrive not on time, but before the said time. Before the deadline. Under the wire. That is why today, tech is leading the charge when it comes to the warehouse sorting process and boosting its power and efficiency. Interconnectivity, thinking outside the box and efficiency is what matters right now. Your process should be flawless, competitive, dynamic, willing to change, and future-proof.
In today’s article, we’ll talk a bit about why your warehouse sorting process is critical to your success, your brand, and your reputation, as well as give you some tips on how to improve it. We will also talk a bit about genetic algorithms and how they are recreating the way managers and auditors are approaching today’s supply chains and various processes.
What is sorting in a warehouse?
The sorting process in a warehouse is the process of organizing products in a way that they can be easily found and picked. It’s an important part of a warehouse’s operations because it helps to make sure that the right product goes to the right customer.
Warehouses use different sorting methods depending on their size and needs. For example, a small business might only need one person to sort all products in alphabetical order by name. A large company might have several people who specialize in different types of sorting, such as food or clothing.
The efficiency of your sorting will be critical to your order fulfillment protocols and metrics. Today this action and step have gained even more importance as customers demand quicker delivery. A recent study and survey uncovered a rather unsettling consumer trend — 69% of consumers indicated that they would be less likely to shop with a retailer if they did not receive their delivery order on time. Not only that, an even bigger number declared that “two-day shipping” simply didn’t cut it. Anything below 24 hours would tarnish their affinity towards that brand. Speed is important, right now, it is one of the most important factors when it comes to e-commerce.
That’s why more and more warehouses and distribution centers are turning to warehouse sorting systems and cutting-edge strategies and algorithms.
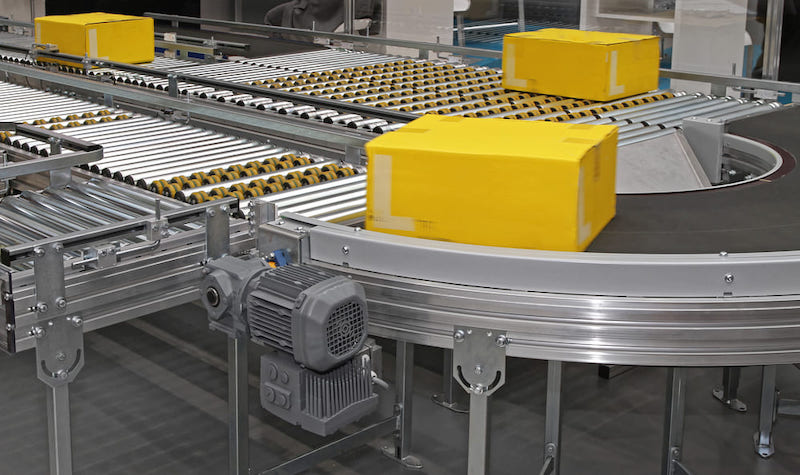
Mutations, fitness, and algorithmic genetics — warehouse sorting 2.0
The shipping industry is evolving. It is still trying to find a way to meet today’s demands, by integrating workers and tech in a balanced and beneficial way. As a result, multiple companies started to seek-out cutting-due solutions to improve customer experiences and revenues — solutions that went beyond AI and drones. One of those, and one that has shown a lot of promise in the last decade, is simulation software. But here’s the interesting thing about these unique software solutions, most have incorporated into their systems genetic algorithms — the very math formula that dictates evolutionary efficiency in nature.
What exactly is that algorithm?
A genetic algorithm as a whole solves multiple tasks concurrently, allowing for a global search for the best outcome and solution. Currently, it is the most used evolutionary optimization algorithm, with several theoretical and practical applications — one of them is in warehouse management.
The algorithm takes various factors and parameters into play — and it can be applied, rather rudimentary, or with much more precise software by warehouse management.
First Phase
The initial population – your staff, your sorters, both human as well as machine – are measured on different values that you need. What each should have to succeed in your environment. And how each connects with the other.
Second Phase
Also known as the fitness phase. Each tool – once again human or machine – is picked according to measurable traits. On objective parameters. Tools are grouped into pairs. Either human with humans. Or machines with machines. Or humans with machines.
Third Phase
Pairs are assigned to workstations. Each pair, due to various factors, have a higher likelihood of success.
Fourth Phase
Pairs that succeed in their settings are broken into individuals — and repaired with new tech or humans. This is the crossover phase, and like in nature, the idea is to create viable fit progenitors for further generations.
Fifth Phase
Also called the mutation phase, warehouse managers need to be on the lookout for alterations — although uncommon in the pairing they do occur at a low random frequency. Sometimes these mutations, or new team dynamics, are advantageous, and they can be duplicated and integrated into the overall algorithm.
Key warehouse sorting challenges
The key warehouse sorting challenges we are seeing today can be broken down into 3:
- the need for accuracy and speed;
- volume and variety of items to sort;
- need for flexibility in sorting methods.
Tips for better warehouse sorting
Sorting is an incredibly complex process. One with a lot of moving parts. It helps to organize the products by category or type so that they can be easily found and shipped. Currently sorting is done manually or automatically. Sorting by manual labor costs more and takes more time than sorting by machine.
The most popular sorting machines are the conveyor belt sorter and the barcode warehouse sorter.
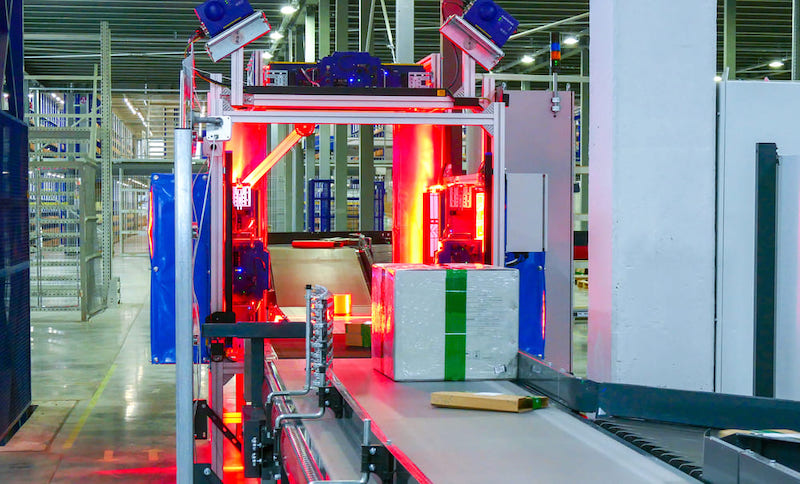
Proper or improper sorting can be crucial for the effective chain of your warehouse processes. It is a step of your order fulfillment that is often overlooked and underestimated, but it can have an enormous impact on your business.
You need to make sure that you are using the right type of sorters for your material and then you need to make sure that they are working in an efficient way. If you want to avoid any possible problems, you should also invest in quality sorting software. You will be able to monitor all sorts of metrics and get alerts if anything goes wrong.
- Organize with popular products in mind — put these items at the forefront of your picking area.
- Understand your whole process — measure and double measure everything. Sometimes an outside POV, an auditor or consulting firm, can do wonders for your operation.
- Improve your tools and staff.
- Edit travel times — 50% of the sorting process are drones or pickers or sorters simply moving around your warehouse. It’s critical to tweak this process by workshopping your warehouse’s layout and getting rid of obstacles.
- Focus on ergonomics.
- Improve your sorting strategies. Use tech and software, particularly during peak seasons.
- Make sure your ERP and WMS are in line and synched up.
A flawless sorting process
There is no such thing as a Goldilocks – just right – warehouse sorting process. There’s just a platform and model that works efficiently right now. Your operation evolves, the times evolve, your third-party suppliers evolve, and your consumers evolve. Nothing stays the same. That’s why it is important to have a dynamic system that can adapt to changing times. A sorting process that is flexible and can easily pivot — one that embraces mutations, new ideas, and innovations. You have to be pliable in today’s industry in order to maintain your competitive edge.
Flow with the change and email [email protected] to stay on top.