With the advance of e-commerce and the way it has changed industries, warehouses are scrambling to maintain their competitive edge. They are employing all types of tactics, strategies, and tools to better their infrastructure and methodology — including strategies for warehouse picking optimization. In this article, we’re going to dive into what picking in a warehouse is, the types of picking available in a warehouse, and why this activity should be a top priority for most companies.
What is picking in a warehouse?
Order picking is a process that involves selecting items from a warehouse or store and preparing them for shipment. For example, if an order arrives at the warehouse, then it is the job of an order picker to find all of the products in the order and ready them for shipment or transportation — including putting them into boxes with packing tape.
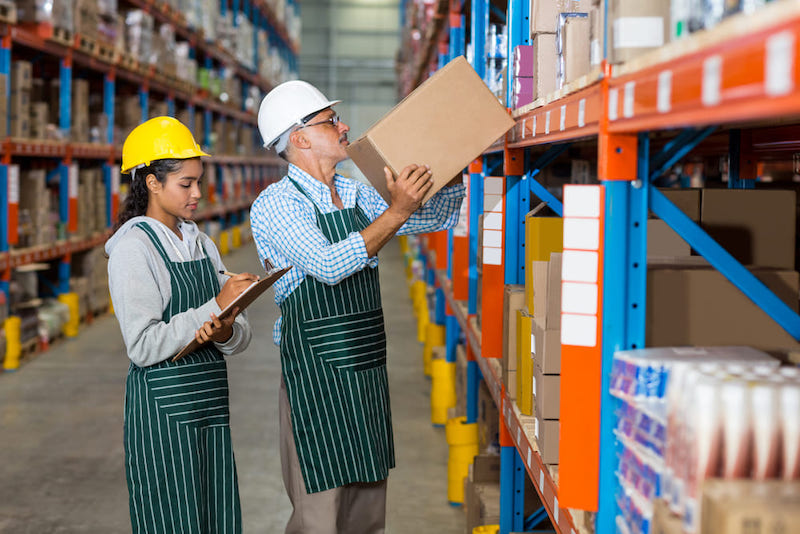
Order picking is one of the most important parts of warehouse operations because it determines how quickly and efficiently items can be shipped. If order picking is not done correctly, it can lead to lost sales and unhappy customers.
For years, this type of operation was performed by humans — very manual, very hands-on. Today, thanks to tech tools and industry innovations, order picking can be performed by drones and other automated systems. In most warehouses, order picking is performed by both humans and robots — both working together to improve metrics and functionality.
In some cases, companies use both humans and robots for order picking because they need to keep up with the demand for products. In other cases, companies rely on robots only because they are more efficient and require less maintenance than humans do.
How to pick orders in a warehouse?
There are many types of pick order systems. But, as a whole, they can be divided into two models with various subtypes. The two major types of picking systems are:
Order Picking System
Order picking systems work by having the picker enter the order onto the system and then the system will move in an automated fashion to find and retrieve that order. These systems are great for warehouses with long rows of shelving, but they can be difficult to use in warehouses with many different products on shelves. Also, these types of systems and models require tech. Amongst them are drones that do the job of the picker. They are fairly new.
Piece Pick Systems
Piece pick systems work by having a picker walk around and grab what they need from each shelf themselves. This is the traditional picking method. These types of picking methods are best for warehouses with lots of different products on shelves but can be slower than order picking.
Types of picking in warehouse
Single order picking
Single order picking is a technique for picking items from a single location. It is the most common method used in warehouse distribution. The goal of single order picking is to minimize the number of times an item needs to be handled during the process of sorting, selecting, and packing orders. Single order picking also reduces labor costs as well as total handling time, since there are fewer items to handle and pickers can work at a faster rate.
Batch picking
Batch picking is a process of selecting products from a group, usually by some kind of randomization. Batch picking as a process has been used for many years in industries such as manufacturing, warehousing, and distribution. This process has been improved and automated over the years to boost efficiency and accuracy.
Multi-batch order picking
Multi-batch order picking is a type of order picking where the items to be selected are grouped together in batches. This allows for more efficient use of space and time. Some advantages of multi-batch order picking are that it reduces the amount of time spent waiting for an item to be picked; It reduces the amount of time spent walking from one location to another; It reduces the number of steps needed to pick an item.
Cluster picking
Cluster picking is the process of grouping items together that are similar in some way. Cluster picking can be used for all sorts of things. In the workplace, cluster picking can be used as a technique to organize orders, or products and make it easier to find what you’re looking for.
Wave picking
Wave picking is an offspring, a variation, of batch and zen picking. It is useful in large warehouses that receive high-volume orders. Items are grouped into sets or waves – how they are called in the industry – according to various factors. Factors and metrics like customer location, order frequency, order type, picking zone, delivery date, etc. Waves are then assigned to pickers and scheduled for better efficiency.
Zone picking
Zone picking divides a warehouse into zones. This is a technique used to speed up the process of picking items from a list. This technique can be used to pick out items quickly, especially when there are many items listed or when an item is not at its designated location on the page.
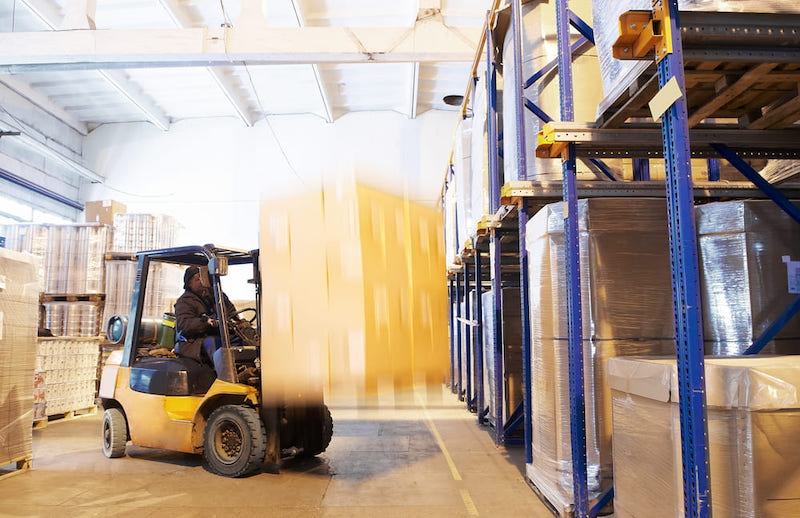
Pick-to-light
This is an automated picking system, It requires the installation of tech — LEDs and barcode scanners on racks and shelves. Once a worker scans a barcode, attached to a shipping carton, the LED on the shelves begins to glow. The worker then flows these lights to retrieve items.
Voice Picking
Instruction sent through a headset, worn by the pickers, organizes workers. An automated system manages each order and tells the worker where to go — this improves accuracy, and speed, since the system itself uses algorithms to calculate better picking strategies.
Mobile scanner-based picking
For this system to work, all items in the warehouse must have a unique barcode. The workers themselves are equipped with mobile scanners that tell them where to go and what items to pick. Pickers scan items as they are picked and if there is an error the software gives them a notification.
Collaborative mobile robots
Drones are now being used in warehouses — they can increase a warehouse or distribution center’s picking speed. They can also augment the capacity of the human workers, helping them out and mitigating picking errors.
Importance of better warehouse picking strategies
Warehouse picking order optimization is critical to the success of e-commerce and retail. It is the backbone of a good distribution center and an efficient operation. As a whole, order picking accounts for 55% of a warehouse’s operational costs — making it one of the most important activities in any center. A strategy that maximizes warehouse order picking will boost a center’s competitive edge and make it not only more efficient but more dynamic. It’s important to evaluate each strategy and understand its importance and overall value for your business.
Stay up-to-date on your warehouse picking and email [email protected] for premier optimization.